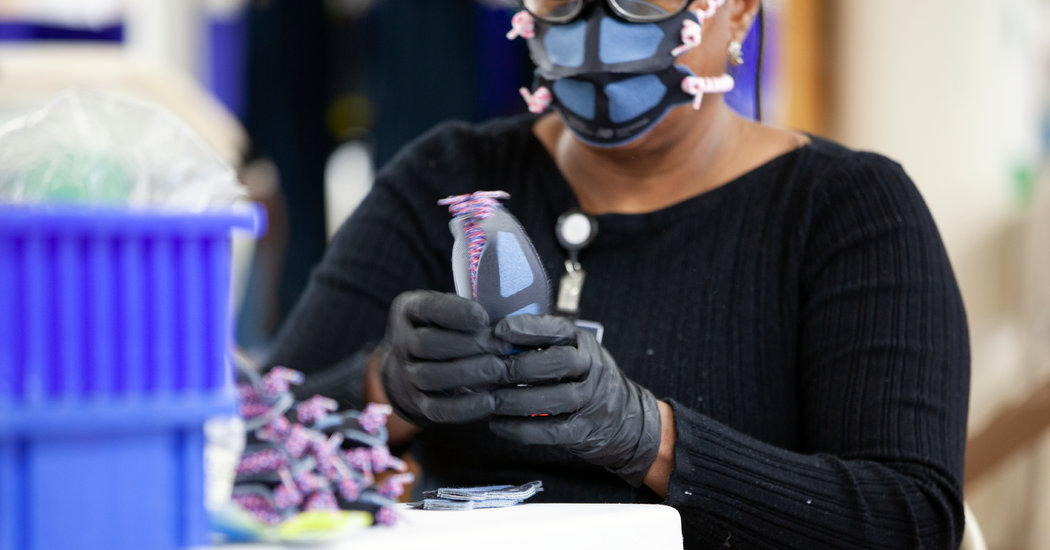
With Games Paused, Sports Companies Shift to Making Medical Supplies
At a pub in London last month, shortly before Britain ordered its citizens to stay home, a small group of life savers shared drinks. It included Rebecca Shipley, a professor of health care engineering at University College London, her U.C.L. colleague, Tim Baker, a former racecar engineer, and some intensive care unit physicians.
On the agenda that night was a discussion to devise methods of handling the deluge of patients infected by Covid-19. The doctors said that the most critical items needed were mechanical ventilators and continuous positive airway pressure machines, or CPAPs.
Baker instantly knew where to turn. In another life he had designed engines for the Jordan Racing team (now Racing Point), a team in Formula One racing. He knew that Formula One teams trained in shaving milliseconds off their race times are capable of producing extremely high quality machinery in a remarkably short span.
The next day, March 25, Baker met with two engineers from Mercedes-AMG Petronas, the leading Formula One team, based in the British Midlands. They had lunch, then worked through the night on a new design for CPAP machines that could be produced rapidly.
Within 100 hours of the initial pub meeting they had a prototype in hand, and within 10 days they had first regulatory approval from the British government to begin production.
“We are approaching 200 already in circulation,” Baker said in a telephone interview from London, “and we have the go-ahead to produce 300 a day for a week and then 1,000 every day.”
Like Mercedes, other Formula One teams are working long hours to accelerate the production of much-needed ventilators, and across athletics many sporting goods manufacturers are repurposing their factory floors and lending their equipment, material and know-how in a widening team effort to fight Covid-19.
“Our company culture is an athletic mind-set,” said Ed Kinnaly, the chief executive of Bauer hockey equipment, which is making face shields for medical personnel. “Our employees viewed this challenge of beating this virus like beating a competitor.”
Bauer, and its sister companies Cascade and Maverik, are based in Liverpool, N.Y., and in Blainville, Quebec. Their factories normally produce Bauer’s hockey skates, helmets and face shields as well as lacrosse equipment. But now they are turning out larger plastic face shields, similar to welding masks, to be used by hospital workers as extra protection against splatter that could contain the contagion.
Latest Updates: Coronavirus Outbreak in the U.S.
- U.S. suffers record deaths, and small businesses struggle to secure loans.
- California buys millions of masks and Los Angeles orders residents to cover their faces.
- Democrats press to double the White House’s newest request for emergency funding.
Kinnaly said one of his engineers approached him last month with the idea. A design was created, the machinery adjusted and soon after production was underway. The company began by making about 3,000 units per week at each location and, as the work force grows more familiar with the process, Kinnaly hopes to ramp up production to 70,000 per week by the end of April.
They are not alone. In Lawrence, Mass., the New Balance athletic shoe company is making cloth face masks for doctors, nurses and hospital staff. Just outside of Oxford, England, the ROKiT Williams Racing team has joined with several other Formula One teams to produce ventilators and in Easton, Pa., Fanatics, a company that normally makes baseball uniforms, is using that fabric — pinstripes and all — to manufacture masks and gowns. Last week, the New England Patriots sent one of its team jets to China to bring back 1.2 million of the desperately needed N95 protective masks while many other sporting goods companies and teams also contribute to the effort.
And it is not just sports. Several other industries, including fashion houses like Prada, Gucci and Eddie Bauer, and perfumeries like Dior and Givenchy, shifted their factory production toward medical supplies and hand sanitizer for the battle against the coronavirus.
In many cases the stories are similar: As people in the Western Hemisphere became increasingly aware of the shortage of vital medical equipment like ventilators, and masks, which help health care professionals guard against infection, people at those companies realized they could help.
“I’m super proud of this team,” said Dave Wheeler, an executive vice president at New Balance. “They’ve put in 18- to 20-hour days solely because the passion is there to fight the battle, and we have the capability.”
Wheeler said he and his technicians have consulted with physicians at Massachusetts General and Brigham and Women’s Hospitals, along with experts at Harvard and M.I.T. to expeditiously produce the best possible masks.
They have retrofitted some machinery and fabrics from their sneaker production, but are also working with new materials, including nonwoven, melt-blown fabrics. Those could help New Balance to provide N95 masks, which block 95 percent of airborne particles that are 0.3 microns or larger, and can be used in emergency rooms.
In Charlotte, N.C., TheMagic5, a fairly new company that produces goggles for competitive swimmers, has been sending custom-built goggles at cost ($15) to several dozen emergency medical workers, nurses and doctors in New York after they send the company scans of their faces. The project is in the early stages, but the initial testing suggests the goggles can be worn by health care professionals for long stretches without pain, adjustment or fogging up.
“I was thinking, how bad would I feel if we didn’t help, if we didn’t even test whether they could work,” said Rasmus Barfred, a triathlete and one of the company’s founders, who lives in New York. “I think a lot of people in sports think that way, too.”
While much of the sports world has focused on producing gear that protects medical personnel, the Formula One effort, nicknamed Project Pitlane, is aimed at helping patients. Covid-19 can cause severe breathing difficulty in its worst cases, but the CPAP machines could help keep people off the ventilators, which are in short supply.
According to Shipley, the U.C.L. medical engineer, data from Italy and China shows that patients who use CPAP machines soon after infection are 50 to 60 percent less likely to need a more invasive ventilator, which also requires sedation.
CPAP machines pump a continuous flow of air through a mask to keep a patient’s airway from narrowing. The Mercedes and U.C.L engineers are still perfecting air flow pressure to minimize oxygen loss as air travels through the new CPAP machines. But that is exactly the kind of engineering challenge that Formula One teams excel at, often making modifications from week to week on their cars through the use of state-of-the-art machinery at their headquarters.
“I’ve been utterly bowled over by them,” Shipley said of the Mercedes engineers. “They’ve been phenomenal, not only with the commitment, but in the speed and quality of what they’ve done for us.”
While Mercedes focuses on the CPAP, engineers from the other teams in Britain, including Haas, McLaren, Racing Point, Red Bull, Renault and Williams, continue work on the mechanical ventilators, conferring and collaborating like never before.
“I’ve probably spoken to my opposite number at our competitors more times in the last two weeks than I have in the last 12 months,” said James Colgate, the operations director at Williams. “The whole grid has come together to help support this project.”
Much of their work is aimed at helping the ventilator manufacturers scale up production at least tenfold — from 25 to 250 per week — and perhaps soon after by a factor of 100. Colgate explained that mechanical ventilators are the size of a shoe box, with 800 parts, some of them tiny; but not as complex as a Formula One car.
“It’s in the DNA of motor sports to find solutions quickly and we are fiercely competitive,” Colgate said. “Now we are just focusing our competitive spirit on this instead. Doing it quickly and safely is what Formula One is good at.”
Vanessa Friedman contributed reporting.